かんばん
JIT生産方式の機能の1つであり、ジャストインタイムを実現し維持するための道具として位置づけられる。一方そのシステムの特異さから「かんばん」だけが独り歩きし、JIT生産方式の代名詞ととらえられがちだが、これはあくまで俗称である。
「かんばん」は、物品目を表示する看板的機能と、その生産情報つまり作業指示を行う伝票的機能とをあわせもつ。よって置場表示である"漢字"の「看板」と区別し、"ひらがな"で表記する。従来の生産情報システムとしてはMRP、統計的在庫管理手法の発注点方式が上げられるが、いずれも安定需要下における予測法であり、情報だけが先行する傾向が見られる。もちろん情報源は"顧客の要求"であるが、工程・業者別に生産計画を立てるため、実際には各々の作業進度が異なり、滞留在庫や欠品等が発生する。また通常、前工程優先の「押し込み生産」の形をとり、たとえ需要変動があっても、一旦作成された生産計画によって造られた仕掛りは"ムダ"となって残る。
これに対し、かんばんでは後工程が"必要な物を、必要な時に、必要なだけ"前工程から引き取る「引っ張り生産」を原則とする。"顧客の要求"をもとにした生産計画によりまず最終工程が作業する。その造った分(引き取りかんばん)を前工程に"引き取り"情報として伝える。前工程は引き取られた分(仕掛けかんばん)だけ補充生産する。つまり後工程の作業進度により生産するため、常に生産計画=実績情報であり、"情報の流れ"と実際の"物の流れ"が一致することになる。
その各工程・業者間における情報交換の道具が「かんばん」で、必ず物についてまわる。いい換えれば「かんばん無しでは物を造れない・運べない」仕組みとなる。品目・数量・作業指示等が明記され、物の流れに沿って存在する。また「かんばんの在る所に"仕掛り"在り」といわれ、かんばん枚数はすなわち仕掛りの量であり、生産の現状を知り現場改革をする手がかりともなり「目で見る管理」としても有効である。
そしてかんばん1枚のロット数および枚数を最少限にし、発行・回収を細分化することが、計画変更に対応しJIT生産を維持する決め手となる。
ルールとしては、①後工程引き取り、②引き取り分前工程生産、③100%良品、④生産の平準化、⑤現物表示、⑥改革ニーズ発見の道具、の6つにまとめられる。
ちなみにかんばんはプレート形である必要はなく、箱、台車、等さまざまな形で応用できる。(図20)
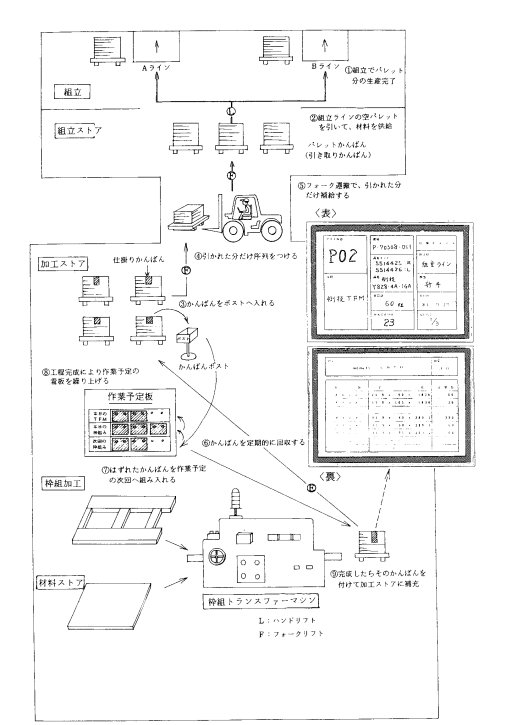
図20 組立と加工でのかんばん運用例